🌟 Introduction
Widely used in cosmetics, pharmaceuticals, household cleaning and other fields, it has become a common choice for packaging liquid products due to its excellent sealing and chemical stability.
In order to ensure the safety and functionality of glass spray bottles in use and to enhance the user experience, strict quality inspection becomes an indispensable link. The goal is to avoid leakage, breakage or uneven spraying due to bottle defects.
This paper analyzes the quality inspection of glass spray bottles and discusses its important role in ensuring product performance and safety. It focuses on the inspection methods and applicable standards at different stages of the production and factory processes to ensure that the products comply with industry specifications and meet market demands.
🌟 Glass spray bottle structure and key quality requirements
Main Components
-
- Bottles: Glass bottles are responsible for storing liquids and need to have good sealing and chemical resistance to prevent the contents from being outsourced or contaminated.
- Sprayer: Includes spray head, pump and connecting tube, responsible for atomizing the liquid and spraying it out. The design of the spray head determines the uniformity and flow rate of the spray, while the pump affects the transfer of pressure from the spray head.
Quality Requirements
-
- Appearance Quality: the surface of the bottle should be free of obvious defects, such as bubbles, cracks, impurities, etc.; the color is uniform, high transparency, to ensure the appearance of the aesthetic and to obtain consumer recognition.
- Dimensional Accuracy: the dimensions of the bottle body must comply with the design standards, especially the diameter and thread size of the bottle mouth to ensure a close fit with the sprayer and avoid poor sealing.
- Mechanical Properties: the bottle body needs to have impact and pressure resistance to ensure that the glass bottle body will not be ruptured due to excessive external force during the whole process of transportation and use.
- Functionality: the spray uniformity of the sprayer and the stability of the spray volume must meet the design requirements to ensure that the amount of liquid sprayed each time the use of the same amount of spray, spray effect is good.
🌟 Glass spray bottle quality inspection items
Appearance Inspection
-
- Visual Inspection: Visual inspection of the bottle by manual or automated equipment to observe whether the surface has cracks, flaws, bubbles and other defects that affect the appearance and use.
- Color and Transparency Inspection: Check the color and transparency of the bottle to ensure that its visual effect meets the design requirements, as well as the visibility and attractiveness of the liquid inside the designed bottle.
Size Inspection
-
- Dimensional Measurement: Use tools such as chucks and gauges to accurately measure the external dimensions of bottles, wall thicknesses, neck diameters, and other critical areas to ensure that the product meets design specifications.
- Tolerance Inspection: Measure the deviation of the actual dimensions from the design standard to ensure that the deviation is within acceptable tolerances to ensure that the match between the bottle and the sprayer and other components is within a certain controllable range.
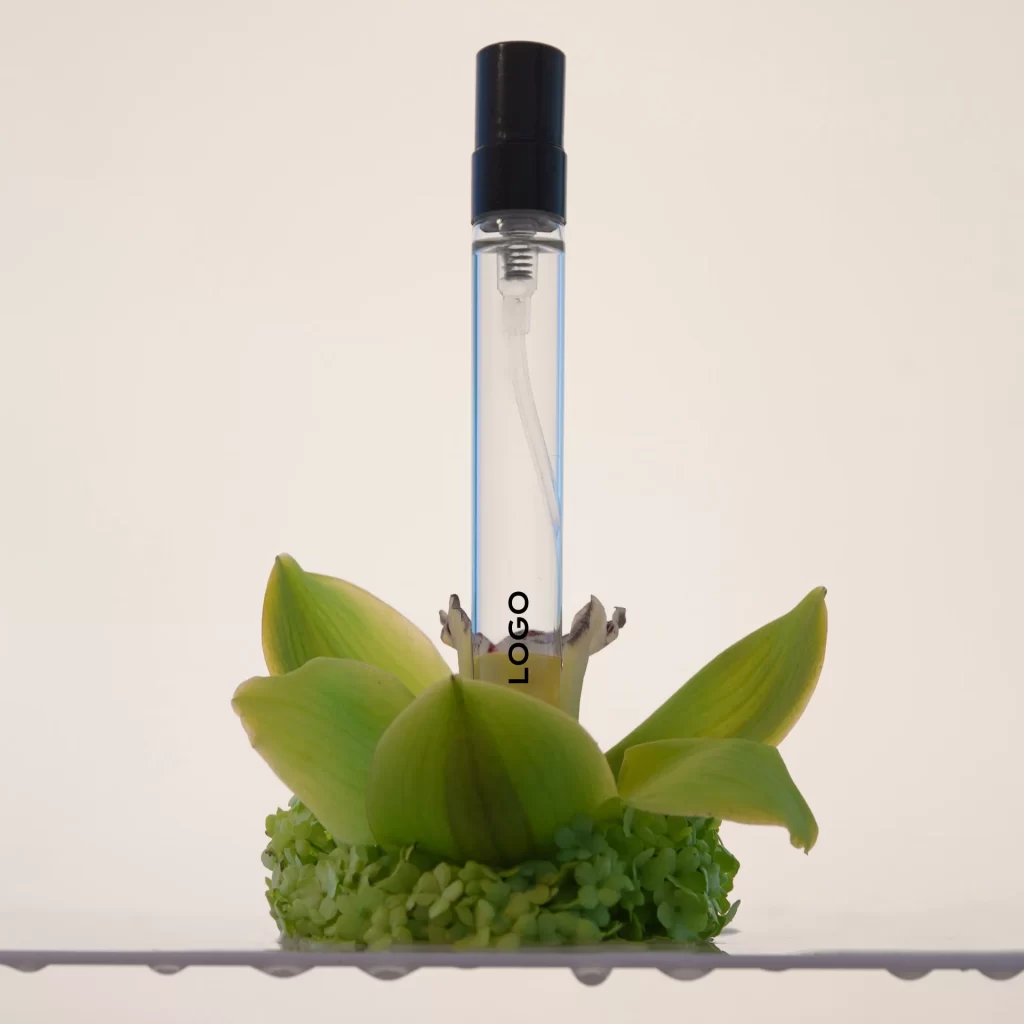
Physical Property Testing
- Impact Resistance Test: Simulate the impact during transportation and use through drop test or pressure test to ensure that the bottle will not break easily under unexpected circumstances.
- Compression Resistance Test: Tests the maximum pressure the bottle can withstand in a sealed state to prevent the bottle from rupturing in a crushed or high-pressure environment.
Spray Function Test
-
- Spray Uniformity: Detect whether the spray distribution of the sprayer is uniform, to avoid spray concentration or ineffective area, affecting the user experience.
- Spray Volume Detection: Use the device to measure the amount of liquid sprayed each time, to ensure consistent spray volume, to ensure the stability and economy of use.
- Leakage Test: Seal test the bottle to verify whether there is any liquid leakage under normal and inverted state to ensure the safety of the product in long-term storage.
Chemical Resistance Test
-
- Chemical Stability: The bottle is tested in contact with the contained liquid to detect whether the glass material reacts chemically with the liquid and to ensure that the bottle will not fail due to liquid corrosion.
- Corrosion Resistance Test: especially for bottles containing acidic, practicing or other corrosive solutions to try to see the test, to ensure that the glass material can remain stable in harsh chemical environments.
🌟 Standards and Criteria for Quality Inspection
National and Industry Standards
Applicable Standards: The quality inspection of glass spray bottles needs to comply with the relevant national and industry standards. For example:
-
- GB/T 2639: Test methods for impact resistance and other physical properties of glass containers to ensure the safety and durability of glass bottles.
- ISO 12870: International standard for specifying dimensions, properties and quality requirements for glass containers to ensure compliance with internationalized product requirements.
These standards provide a unified reference for production and quality inspection, which helps enterprises standardize production and ensure product versatility and compliance in different markets.
Enterprise Internal Control Standards
Establishment of Internal Control Standards: In addition to national and industry standards, companies usually set stricter internal control standards based on the specific use scenarios and market demand for their products. These standards may cover:
-
- Higher dimensional accuracy is required to ensure seamless joining of different components.
- Stricter spray uniformity and spray cooler stability to enhance the user experience.
- Higher impact resistance and chemical resistance to adapt to special transportation environments or the need to hold special liquids.
By developing internal control standards, companies can improve the competitiveness and reliability of their products and adapt to the individual requirements of different customers.
Sample Inspection vs. Full Inspection
-
- Sample Testing: Usually applied to quality testing during mass production. Through statistical methods, some samples are randomly selected from the production line for testing, and the testing items include appearance, size, physical properties, functionality and so on. Sampling inspection is applicable to routine products, which can improve testing efficiency and save costs.
- Full Inspection: All-round inspection of spray bottles produced every day to ensure that each product meets the quality inspection requirements. Full inspection is usually applied to high-end or products with particularly high safety requirements, such as pharmaceutical grade products or special chemical containers.
🌟 Quality control and improvement
Feedback and Analysis of Inspection Data
Feedback Mechanism: Quality inspection is not only to detect obvious or potential problems, but also an important part of improving the production process. By providing timely feedback of inspection results to the production line, companies can effectively identify defects and bottlenecks in the production process. For example:
-
- If substandard bottle dimensions are detected, the molding process parameters can be quickly adjusted.
- In case of unstable spray function, the assembly precision of nozzles and pumps or the quality of raw materials can be checked immediately.
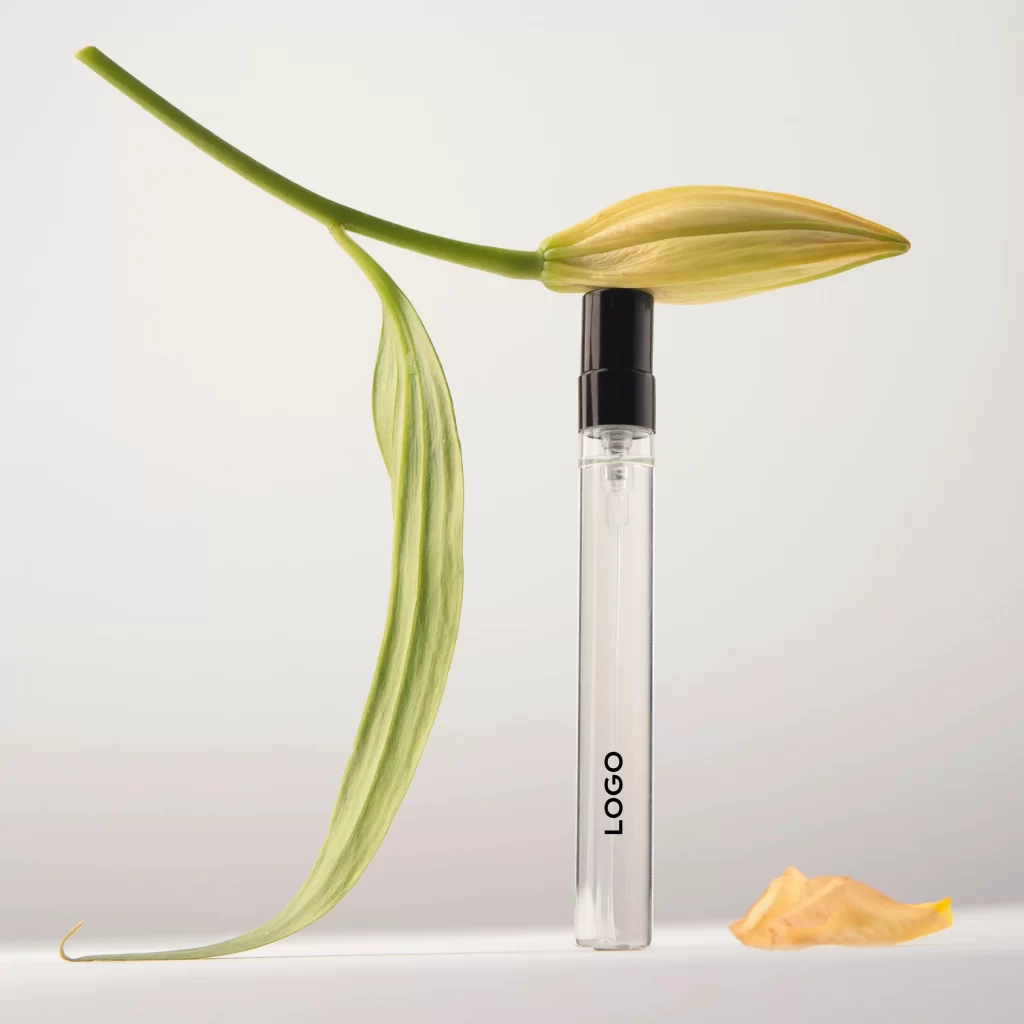
Data Analysis: By systematically collecting and organizing inspection data, companies are able to identify trends and potential problems in product quality. For example:
-
- Analyze the pass rate of different batches of products to find out which process links or equipment are prone to fluctuations.
- Use statistical tools to analyze problems that will recur in the production of products.
Quality Control during Production
Monitoring and Regulation of Critical Steps: In the production process, quality control should be carried out throughout each critical step in order to prevent problems from accumulating and magnifying in subsequent steps. Example:
-
- Bottle Molding Process: real-time monitoring of temperature, mold pressure, cooling time and other key parameters to ensure the accuracy of bottle size and wall thickness.
- Sprayer Assembly Process: monitor the assembly accuracy of spray nozzles, pumps, tubes and other components through automated testing equipment to avoid affecting the spray function.
- Packaging and Sealing Inspection: During final packaging, final confirmation of bottle sealing and appearance is carried out through sampling or full inspection to ensure the integrity of the product before leaving the factory.
Through these real-time monitoring and feedback mechanisms, companies can make timely adjustments during the production process to ensure the production of high-quality glass spray bottles, reduce the generation of defective products, and improve production efficiency.
🌟 Conclusion
The quality inspection room for glass spray bottles is a critical part of ensuring that the product remains reliable and safe in all types of applications. Through rigorous testing of appearance, dimensions, physical properties and functionality, problems in use due to bottle defects or functional failures can be avoided. Quality inspection not only improves product qualification rate, but also enhances users’ trust in the products and ensures their safe and stable use in cosmetics, pharmaceuticals and other fields.
With the continuous progress of emerging technologies, the efficiency and accuracy of quality inspection will be further enhanced. In the future, it can be combined with more cutting-edge intelligent inspection technologies, such as ai image recognition and automated inspection, which can detect product defects more quickly and accurately, and reduce the error of manual inspection. These new technologies will help realize the full automation and real-time quality control of the production process, and promote the glass spray bottle manufacturing industry to a more intelligent and efficient direction.
Üsküdar su kaçak servisi Üsküdar su kaçak tespiti hizmeti ile, su sızıntılarına profesyonel çözümler sunuyoruz. Su kaçakları artık sorun değil! https://astronomyfriends.com/read-blog/1982
awesome
Thank you.
webpage https://skinsli.com/products/real-barrier-extreme-essence-toner-light-200-ml